Do It Yourself Vacuum Forming For The Hobbyist Pdf Viewer
I recently needed 12 fake candlestick phones for a musical ('Crazy For You'). Real candlestick phones are incredibly expensive, and even replicas were too much for my budget.
All 12 needed to match as well. I decided to make them all. I wanted to match the shape of the bases to the real thing, but it would take too long to sculpt 12 bases, and casting them would be too expensive.
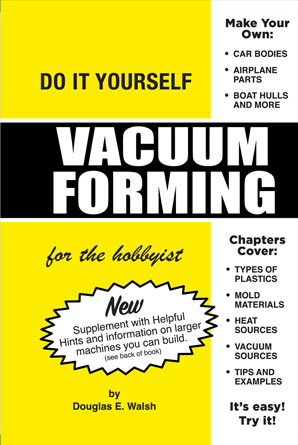
It looked like it could be vacuum formed. I've worked with plastics in the past, but never with a vacuum former, though I've seen some in action. I couldn't spend a lot of time or money building a vacuum forming machine for this project; I figured if I liked what it was capable of, I would build a nicer one after this project based on what I learned. After researching what I needed, I found I could build one for free. I already had the necessary components in my shop. I figured many prop makers will already have these parts as well, so I am sharing how I did it. Step 1: Gather Your Materials and Tools.
For me, this vacuum forming machine was free, but that's because I already had all the tools and materials. These include: * a shop-vac * a heat gun * some scraps of MDF * some scraps of lauan * spring clamps The tools I used were a drill press, a table saw and a small hand saw, a combination square and a pencil.
I also used a bit of glue and some grid paper. You can substitute some of the tools used as well as the precise materials needed.
Tangible things can be bought. Professionals can be hired to build and repair. Artists can be employed to decorate or customize. Nevertheless, people all over the world continue to create and modify. This time, computer hobbyists also formed communities to create. Kramer in 2007, Craftster allows everyone to view the.
The shop-vac I had cost $25 new, and the heat gun was $25 new as well, both from the big-box hardware store. So if you had to buy everything for this, it would only be $50 for the equipment and a couple bucks for the materials. Even if you never vacuum form again, you can still use the shop-vac for cleaning your shop and the heat gun for other projects. The plastic I was using was a thin sheet of Sintra, which is a brand of expanded PVC. It was about 2-3 mm thick, and I cut it into smaller squares using a utility knife and a straightedge.
Step 2: The Top of the Platen. For the top of the platen, I cut a square of 1/2' MDF to 8 inches by 8 inches. You can make it bigger or smaller if you want; I made mine as small as possible for the pieces I was making. That way, I would not have to use a giant sheet of plastic for each item.
I used MDF because it gave me a nice smooth and level surface for the top, which is an advantage in vacuum forming. You can substitute other materials, such as 3/4' MDF or even a piece of melamine board. You do want to be careful about using painted or coated pieces, as the heat of the plastic may melt or burn these. I drilled a grid of holes through the MDF.
I taped a piece of grid paper to the top to make the layout easy. I used a 1/8' drill bit; you do not want the holes to be too big.
I left an inch undrilled around the border; this is where the frame will sit. I ripped some 1/4' MDF strips to 1 inch wide and glued them along the perimeter of the bottom of the platen. Make sure to fit these tightly together so no air can escape through the joints.
I then drilled a large hole with a spade bit in another 8' by 8' square of 1/2' MDF. This hole was just large enough so I could shove the end of my vacuum hose in and it would stay in place. I attached this MDF square to the other side of the 1/4' strips, making a 'sandwich'. The empty cavity in the middle of the sandwich allowed air to be sucked into each of the tiny holes when the vacuum cleaner was turned on. Step 4: The Frame. I was ready for my first test. I grabbed some random objects and arranged them on the platen.
I was using some Sintra plastic (expanded PVC) for my vacuum forming I had left over from a few years ago. I think it's about 2-3mm thick. I clamped it inside the frame and heated it up with my heat gun for a few minutes until the whole piece was very flexible.
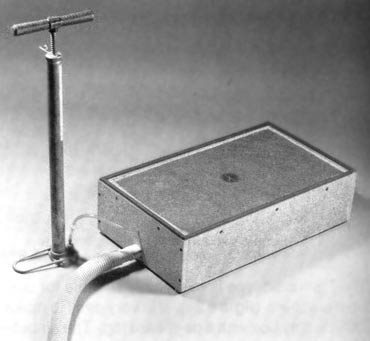
(While writing this Instructable, I also learned that Sintra can be softened by submerging it in boiling water for 10 to 15 seconds, which seems like it would heat it more evenly). When the Sintra is fully heated, turn on the vacuum cleaner and place the plastic over your objects onto the platen. The plastic will stretch as it lays over the objects; when the frame touches the platen and creates a seal, the vacuum will be able to suck the plastic tightly over the pieces. Make sure to bring the frame straight down rather than from the side, or you may stretch parts of the plastic and cause it to tear. I found if the plastic does not pull as tightly over some parts as you would like (either because the plastic was not heated enough in that spot, or because the vacuum is not strong enough), you can heat it up some more with the heat gun as the vacuum is still running. With plastic as thin as I was using, it was really easy to burn holes through the plastic if I heated up a spot for just a split second too long. Step 6: My First 'pulls'.
The model for the phone base itself was built up out of a few layers of MDF and plywood. I used Bondo (a thick type of polyester resin used for auto body filling) to smooth and refine the surface. In bigger and more powerful vacuum forming machines, you want to make sure to build your models out of something strong and solid because materials like Styrofoam can be crushed under the pressure. For a machine this small and weak, that probably won't happen. You should also avoid materials that will melt or deform under heat. I wanted a clean edge along the bottom; I raised the model up a bit so the plastic would be pulled underneath it a little bit. I used 3 tiny pieces of MDF to hold the model up without covering any of the air holes.
The model I built was just a bit too big for this vacuum forming machine. If I were to do this again, I would make the platen 2 or 3 inches bigger on each side. A vacuum cleaner is a really weak source of vacuum. If I were upgrading this machine, that is the first thing I would replace. I found that after I placed the plastic over the mold, I could use the heat gun to heat the spots which did not get sucked down all the way, so I was still able to get all 12 pieces out of this machine. What a great Instructable.
I too occasional built props as well as doing scenic design and construction for schools and local community theaters. I've always been fascinated with vacuforms. I will archive your instructable for future reference. Years ago, while searching props on the web, I came across a website that offered instructions for building an actual vacuform table, complete with heating coils and a hinged frame for moving the heated plastic from the heat bed over to to the platen/vacuum bed. It was build to one of the plastic industry's standard sheet size (I believe about 48'X60'). Sadly, by the time I was in a position to build one, I could no longer find the website. I was also in need of candlestick phones, years ago, for a production of 'Cabaret', and I ended up building them out of parts cannibalized from thrift store table lamps.
I wish I'd had your instructable then. Keep up the good work! TheStarWizard PS If anyone comes across instructions for building a large vacuform table that doesn't require putting the plastic in your stove's oven, please let me know. If one could achieve a perfect vacuum, this would amount to slightly over one BAR or about 30 inches pressure. This barometric pressure is often seen on Tee Vee when the weather is announced.
A vacuum pump could never 'pull' more than this because the air pressure of our atmosphere that is actually doing the pushing hardly goes above one BAR. Standard atmospheric barometric pressure is given around 1013 millibars, or 1.013 BAR. As another example, If a person 50 ft above a jar of water sucks a 'perfect' vacuum using a 50 ft straw, the highest the water will go up the straw is about 34 feet (at sea level). Any water column taller than 34 feet would weigh more than the weight of the atmosphere (14.7 lbs/sq in) that is pushing the water upward. Imagining a one inch by one inch square tube filled up to 34 feet will weigh about 14.7 pounds if one uses the weight of water (about 62.4 lbs/cubic foot). A simple calculator works wonders here. This info is not necessary for the project here but the info revealed here might be interesting to some.
The plastic I was using was.030' thick. It has no special features other than it has to be a thermoplastic (one which becomes flexible when heated and rigid when cooled back to room temperature). Styrene is one of the cheaper types, making it popular with prop makers doing vacuum forming. Others include PVC (vinyl), Kydex (a brand name for an acrylic/PVC copolymer), ABS, CAB, and acrylic (plexiglass). You can also use PET and polyethylene, which you can get from soft drink and milk bottles, but these are extremely difficult to paint or glue to. I'm a little late in posting but modifying the reed valves on a small cheap automotive compressor might do the trick for producing a strong vacuum.I have seen a very small unit on a job site used to align two pieces of granite together for counter-tops,and it was no larger than a 12v air compressor to fill your tires.I repair my own compressors and found they use reed valves to maintain constant psi.why not reverse the process for vacuum. It might require some mod.like an added check valve.I'm curious if anyone has tried it yet.
A more powerful vac would make it better, but from what I've read, a larger shop vac is not more powerful than a smaller shop vac. Larger and more powerful shop vacs move more air in less time than smaller ones, but the amount of vacuum pressure is still between 2 and 6 inches of Mercury.
Also, while a heat gun is usable on smaller pieces like I was doing, when you start getting bigger, you want more of an even heat, like with an oven. Even with a powerful heat gun, you'll end up heating one section until it is pliable enough for forming, and when you move to heat up another section, that first section will cool back down. I had a thought of building a small 'hot box' to hold my plastic while I heat it (maybe just an enclosed box lined with aluminum foil) so the heat will not dissipate so quickly as I use my hot air gun.
Still, my next step would be to build a better heating system because using a hot air gun really limits the size and thickness of plastic you can use. Good thoughts Eric. I can see the vac thing as you say. I have the big shop vac and a smaller (9 gallon) ridgid shop vac and i tend to like the smaller one more.I never even thought to see which one has more suction. A Hot box.thats an idea. Like you say, build it, line it with something shiny like tin foil, use that tin foil tape to close all the seams then, build a bigger version so you can insulate the smaller one, put the bigger one over it so you shouldnt lose any heat.
You would probably need one heat gun on each end though. I wanna try this and see what I can make.lol. A possible shortcut is to use pegboard as your forming surface. You will want to seal smooth any non-through holes at the edges, a piece of aluminum tape along that area may do the job. If you need to vacuum form larger objects, it's going to be a lot faster than drilling out a 2'x2' board.
However you will probably want to put in supports between the pegboard and the bottom of the vacuum chamber to prevent the pegboard from flexing. Since most pegboard is substantially similar to masonite, it should not be significantly impacted by the heat. If you find that the spacing on the pegboard is too wide, you can always grid out additional holes between each of the holes in the space you need the work done in. Finally if you need to vacuum form smaller pieces of plastic than your form would normally allow, a sheet or two of masonite could be used to mask off portions of the vacuform board that will not have plastic over them. $99 Shark Vacuum cleaner is quite useless as a vacuum cleaner but should work great for this project. Let me explain, Shark vacuum as you often see in their TV ads shows how capable this vacuum is but in reality, the motor pass a low CFM of air with very high negative pressure - a mistake many vacuum machine manufacturer did thinking this will make the vacuum work better. This is also why you see them advertising how strong the 'suction' is 'when in sealed vacuum' where no work is performed.
For a vacuum system to work properly, it needs to pass a very high amount of air through, look at the commercial carpet cleaner truck, their vacuum not only produce negative pressure but pass very high amount of air. We called CFM - Cubic feet per minute.
Now in vacuum forming, we do not need large amount of air to go through but instead we need the negative pressure the vacuum can create. Just happened the shark vacuum can do this quite nicely. I was going to mention the venturi method of pulling a vacuum using an air compressor at 30-40 PSI to drive it, but I see someone has posted all the details. This is an excellent method of creating a very good mid-range vacuum for experimental purposes, although a bit noisy, LOL.
The 2nd comment was to wonder if there would be any value in having a soft rubber (or other soft, compressible, airtight material) gasket between the bottom of the two-part piece that holds the plastic to be formed, and the vacuum plate. Even stick-on weatherstripping might work, although getting a tight seal at the corners would require some careful work. #3 - Would a couple or three 'heat lamps' - 150 watt bulbs, I think, with built in reflectors and a reddish face - aimed at the top of the platen be of any use in keeping the plastic at a more flexible temperature during the actual forming process? The heat is diffused, but strong. They would allow full access to the piece being worked. I use one to pre-heat the cylinder head on my snowblower when it's -30, and it's very effective.
(I think they sell these bulbs for use in bathroom/shower ceiling fixtures). An alternate source of vacuum is an old refrigeration compressor. Not all compressors will work for this - I happen to have a couple of ancient ones in my shop.The simplest test (if you don't have a vacuum gauge) is to put your thumb over the intake pipe and switch on. These units will pull quite high vacuums - the disadvantage is that the volume of air moved is low. Be careful - if it is a 'suck' type without a relief valve, you can get a blood blister very quickly.
One option might be to start with the shop vac or venturi vacuum source to exhaust the majority of trapped air, then stop off that hose opening and start up the refrigeration unit, connected separately to your base-plate assembly, to pump it down further. This is probably beyond your requirements, but I mention it as I've used them as a vacuum source for other projects, with good success.
Loved this Instructable. I can see all sorts of possibilities - custom-forming covers for small home-brewed electronic or electro-mechanical devices, for instance. Thanks for sharing. I see the earlier poster added a link to a commercially available venturi vacuum source that connects to an air compressor. However, if you're cheap, or broke, a search of the online archives of a) Popular Mechanics b) Popular Science, and c) the British publication 'Model Engineer' will turn up several different articles on how it's done and what the critical dimensions are. If you're searching 'Model Engineer' index, you'll find a lot of info under articles on 'Injectors' - used to force water finto the pressurized boiler of a steam locomotive, driven by steam.
Boiler pressures can exceed 200 P.S.I., so the injectors can operate at far higher levels than you'd need for vacuum forming. However they have the advantage that they can be shop-built rather than purchased. I made one low-pressure experimental one, run on compressed air, using two disposable plastic cones from the instrument doctors use to look into patients' ears. Being a cone-within-a-cone venturi, and although normally used with water, they can be adapted for other things. I know this adds cost to the set up but if willing to take the $85 plunge, adding a venturi with compressed air (might need a compressor as well, anywhere from free to $50) can get you up to 26' of Hg. If not familiar, just hook up an air compressor to the venturi with around 30 psi continuous (very common pressure) and hook one end up to the vacuum plate.
My buddy used to use this to create vac plates sometimes 12' x 18' large for vertical and horizontal CNC machining applications where huge cuts were being taken and the parts never moved (strong vacuum). Nice Instructable! Simple and to the point. I'm curious about where you source your plastics? I know you said you used excess that you already had. I've always had trouble getting plastic when I need it.
Just a couple of notes: 1) if you make the holes in your surface smaller you can get a more even and more detailed form. For example, if you halved the drill bit size, and doubled the number of holes (other than creating more work for yourself in drilling) the 'resolution' of your form increases and the detail and continuity between formings gets better. 2) To get more detail in the forms you can drill small holed through your original model around detailed areas (for example in the holes of the rotary dial on your phone) these small holes give more suction in those areas and pull the plastic in firmer and into places where there might otherwise be bubbles, just be careful not to cause the model to get stuck in the plastic when it cools, or to make holes too deep and put holes in your plastic! Hi RandomIdeaMan, Thanks for the tips.
I'll have to try more/smaller holes on my next version. I did have some holes drilled throughout my model on the concave parts; I added a bunch more after my first test. As far as buying plastics, I've always found Googling your local area for plastics fabrication/supply shops is useful. These places usually seem to be located off the beaten path and few of them have websites. But if there's one within a reasonable driving distance, the price is almost always cheaper than what yo can get online, particularly with shipping prices for large sheets. Your big box home improvement stores will have acrylic sheets, and the 'For Sale' and 'Garage Sale' signs they have are usually styrene, which is a good plastic for vacuum forming.
Craft stores like Hobby Lobby and Michaels usually don't have anything useful, but if you can find hobby/model airplane or train stores, they may have small sheets of styrene in a variety if thicknesses. Sign-making shops may be willing to let you have off-cuts of vinyl and other plastics they use, or may let you know where they get their plastic from.
Personalized Fake and Joke Newspapers and Personalized Newspapers and Personalized Headlines for Gags and Gifts, Birthdays, Movies and Plays, Advertising, Publicity Stunts, Baby Showers, Wedding Showers, Stag Parties, Corporate Recognition, Awards, Thank You's, Revenge, Make a Point, Birth and Death Announcements, Wedding and Marriage Announcements, Practical Jokes, Cerebral Terrorism, Personalized Birthday Gags, Gifts. Fake Newspapers available in Small (pocket clipping) size, Full single page, Whole newspaper, Giant Poster, and Tabloid (by special request)..
TrixiePixie Graphics®, Channel54News®, and the 'Resting Bird' graphic are Registered Trademarks. TrixiePixGraphics™, National-Media™, and FakeNewspapers™ are Trademarks of TrixiePixie Graphics®. This material may not be published, broadcast, rewritten or redistributed. Ezvid Full Offline Installer Download more. TrixiePixie Graphics®, Channel54News®, TrixiePix Graphics™ and FakeNewspapers™ are Protected under US and International Law. Copyright © 1982-2016 TrixiePixGraphics.Com®, www.fakeababy.com www.fakeultrasounds.net www.dryerasechecks.com www.fakenewspapers.com All Rights Reserved. All Rights Reserved.
Download Lagu Endless Praise Planet Shakers. ® Novelty Gifts and Gags that will Shock and Surprise the People You Love - - - - - - - - - - - - ™ ® Illegal to publish, broadcast, rewrite or redistribute -- Copyright © 1982 - 2013 TrixiePixGraphics ™All Rights Reserved Our Websites Feature Exclusive and Copywrited Artwork None of Our Products are Duplicated We Provide One of a Kind Originals Created by Our Paid Artists We have a NEW Website! Please Visit Fake News Papers Fake News Videos A Few Abbreviations.